Table of Contents
Lithography: what is it, and how does the lithographic process work?
What is lithography? And how does the lithographic printing process work? Today we’d like to look in detail at an ancient technique that is still very much alive today. We’ll begin with the etymology of the word lithography, as it provides a big clue as to the main protagonist in the technique. After that we’ll look at the various stages of the process, and finally see how it has changed through time. Piqued your interest? Then read on!
What is lithography?
Let’s start by looking at the word itself: it comes from the Greek and stems from a combination of two terms: lithos, which means stone, and ghafhé, which means writing. So there you have it: the key material in the process is stone.
The lithographic process was perfected in 1796 by Alois Senefelder (Prague, 1771 – Munich, 1834). The technique was widely used (and, indeed, still is) in the art world, as it allows multiple copies to be made of hand-drawn illustrations, including in colour. Huge numbers of artists have created wonderful lithographs over the centuries, including Georges Braque, Marc Chagall, Salvador Dalí, Francisco Goya, Paul Klee, Édouard Manet, Joan Miró, Edvard Munch and Pablo Picasso, to name but a few.
But how does this ‘chemical’ printing process work? Let’s take a look.
Inside the lithographic process
The principle that underpins lithography is a simple, widely known chemical fact: that water and fatty or oily substances repel one another. With that clarified, we can now delve into the process in more depth without getting lost.
Lithographic limestone is extracted from the quarries of Solnhofen in Bavaria, and made almost entirely of calcium carbonate. Its special features are its hardness, its extremely fine grain and its very high level of porosity, meaning it absorbs water easily. The perfect stone for printing should be free from defects, have an extremely smooth surface and be at least 6 cm thick to minimise the risk of breakage. The slab is cut into rectangular sections, the surface is smoothed down and the edges are chamfered.
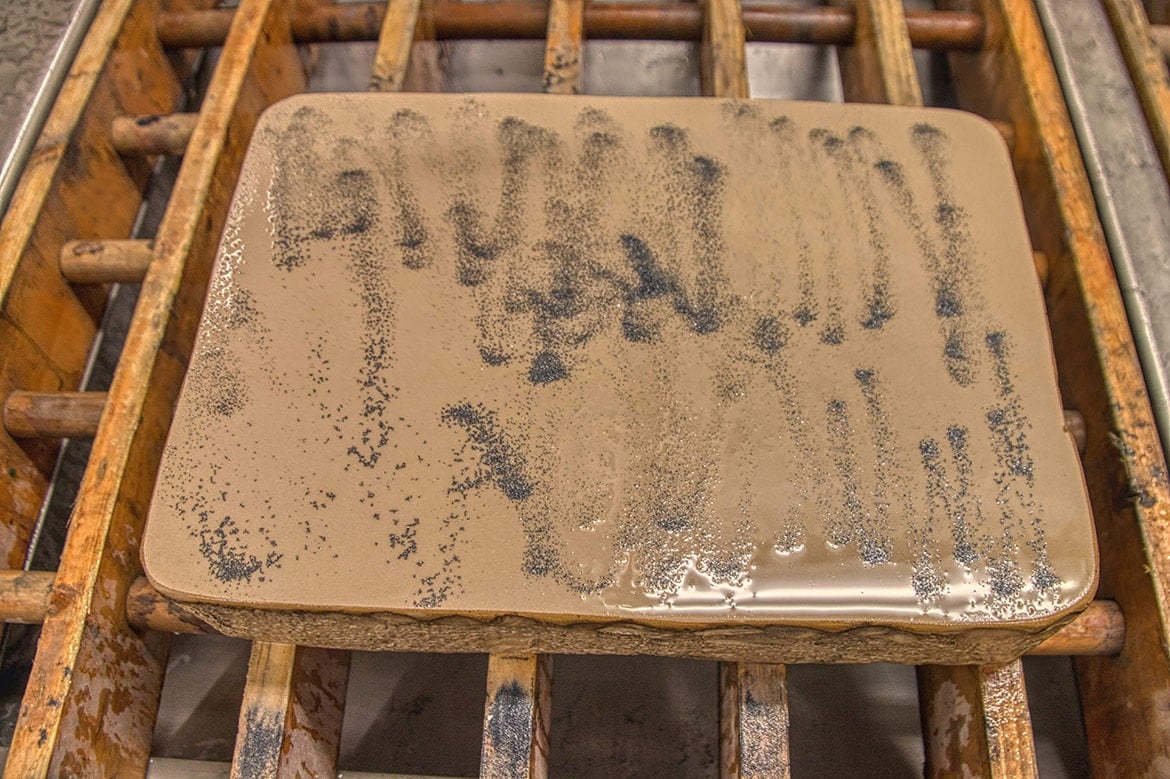
What you can see here is a lithographic plate. The image is drawn on the surface with pencils made of fat or resin. The stone is then sprinkled with talc and dampened with a solution of acetic acid and gum arabic: the acetic acid helps the image stand out, while the gum arabic increases the resistance of the stone to the fatty substances. The plate is then washed and, when still damp, inked with a roller. At this point a chemical reaction takes place: in the areas not covered with ink, the acid transforms the calcium carbonate in the stone into calcium nitrate, which has water-repellent properties, while the calcium carbonate retains the ink on the drawn part.
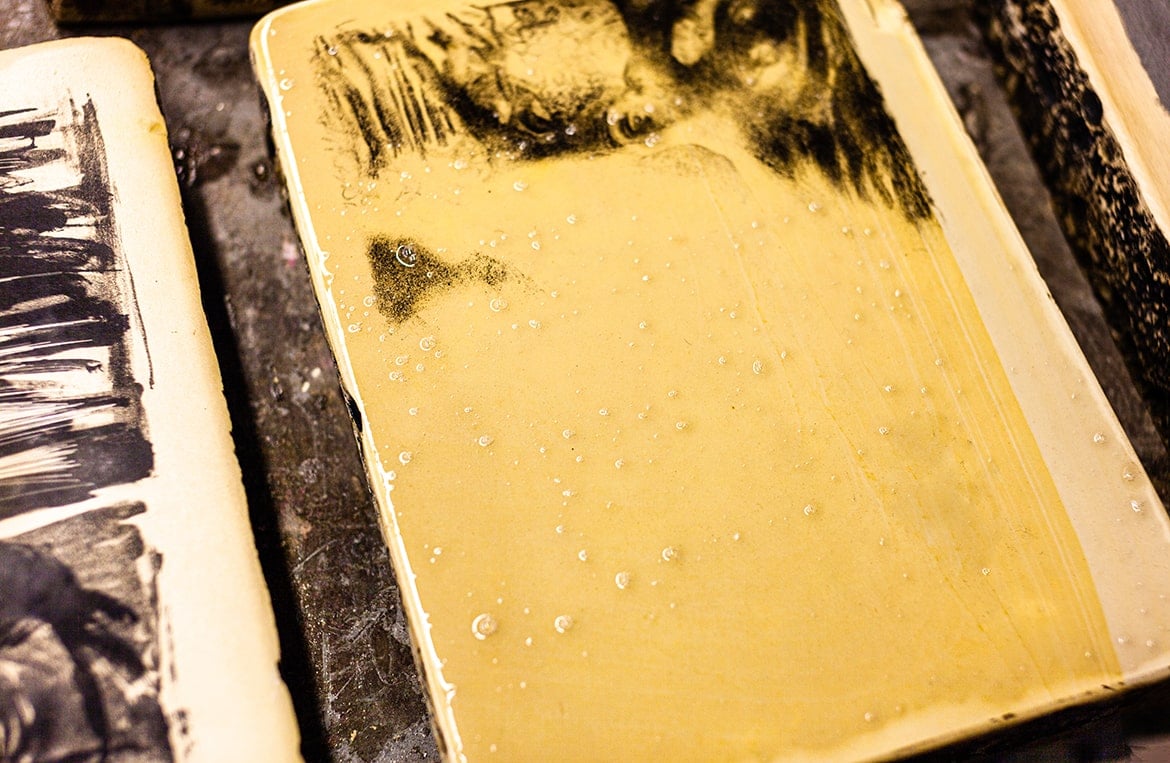
A sheet of paper is then placed on the plate and pressed, so the design is transferred onto it, producing the first lithographic print, with very clear and precise lines. This process can be repeated again and again, even hundreds of times, by inking and dampening the same plate.
You can see the result here. This is a lithograph by Benedetto Eredi (1750-1812), entitled Jesus Before the Crucifixion.
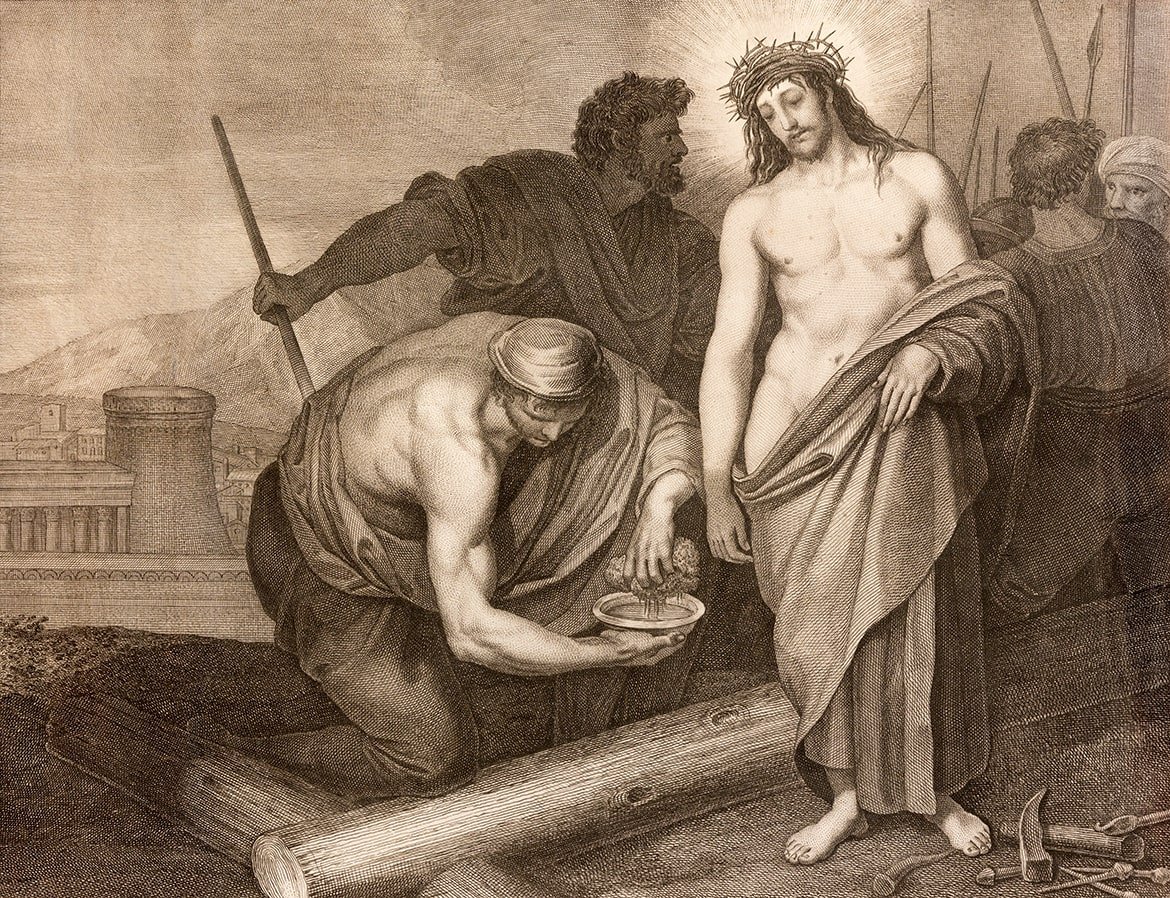
As we mentioned above, lithography can also be used to reproduce colours (up to thirty in the same work), and this led to the technique spreading not only in the field of art, but also for printing posters and for book illustrations. Chromolithography, as it is known, is a very laborious process, as a plate, with the design drawn on it perfectly, has to be produced for each colour to be added to the work. Naturally, the more colours there are, the longer the process becomes.
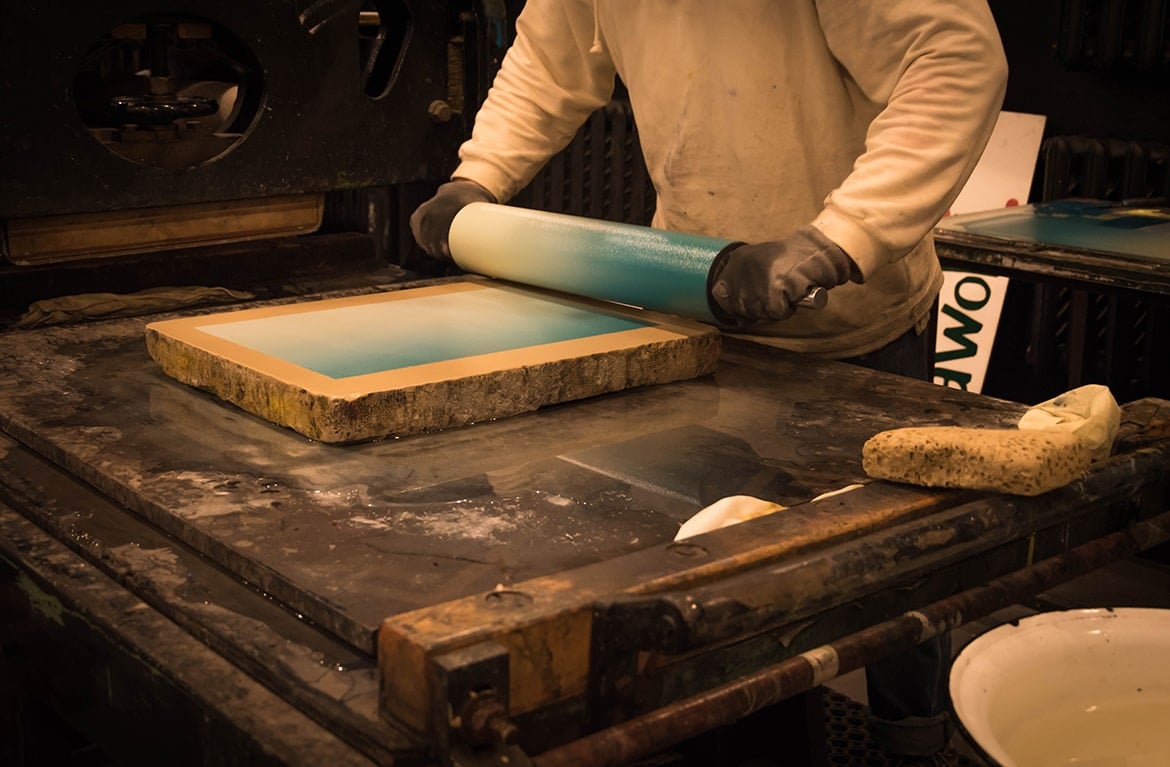
Up to now we’ve been discussing the original lithographic process, but some tweaks have been made to it over the years to make it faster and more convenient. The biggest change regarded the lithographic limestone itself, which was a difficult material to handle, heavy and liable to break. For this reason, instead of stone, zinc and aluminium plates are now used instead, and still ensure a perfect result. As tradition dictates, the techniques take their name from the materials used, so we talk about zincography on zinc and (albeit rarely) algraphy on aluminium.
Want to discover more interesting facts? Go to the World of Printing section of our blog, where you’ll find lots of other articles about printing’s past and present. Enjoy!